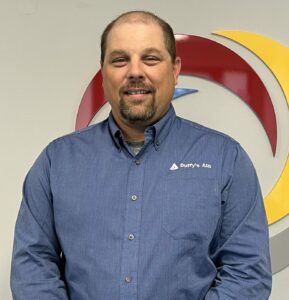
Paul Pumputis
Service Manager, Duffy’s AIS
Tech Support
Technical support is just that, support. It is not a replacement for proper troubleshooting or preliminary legwork.
Very often, techs are using this resource as more of a shortcut instead of a tool to help prove their own findings. I have heard from tech service personnel that one of their pet peeves is the technician that calls in on his way to the service call. They tell them what the complaint is and ask them, “well, what do you think?”.
As service technicians, we need to make sure we are doing our part first. Tech support relies on us to be their eyes and ears in the field, and we rely on them to be our experience where we do not have any; after all, experience is something you get after you need it.
I once had a customer years ago with a countertop conveyor oven. The complaint was that it would not turn on in the morning. This could be several possibilities, supply power, power switch, control limit, poor wiring connection, but without any context, it would be impossible to pinpoint a diagnosis. Let me add some information. Upon the initial visit, the control box high limit was tripped. It is a manual reset inside the control box, so the customer does not have access to reset it. I reset it and checked the likely reasons for it to trip. Cooling fan operation, cooling fan thermostat, clogged air vents, everything checked out. This limit only tripped occasionally, so I figured I had a limit that was dropping off early, and I replaced it. A week or two goes by, and we get the call for the same issue. What did I miss? Now I go back and double-check everything. My voltage was correct, so I don’t have an issue with high wattage output causing overheating. My amp draw confirms that as well, with a little help from Ohm’s Law. The cooling fan is still running strong, and all my air vents are clean as a whistle. Frustrated, I make the call.
When you speak with factory techs, I feel it is very important to verify that you are a technician calling in and not an end-user or a maintenance person. I do this not by stating it as fact but by giving them all the information I have, clearly and in proper terms. Anyone that knows me knows how I feel about this. Voltage is not good or bad. It is a number followed by AC or DC, and sometimes milliamperage is not in spec or out of spec; it is a number followed by Amps or Microamps.
Gas pressure is not fine; it is a number followed by inches of water column. Giving that number with proper denotations demonstrates a level of knowledge and, in most cases, gets you some respect from the person on the other end who now knows they are able to help you.
Back to my oven, I tell the factory tech my issue. I have 208 volts AC, it’s single phase, and I am drawing about 27 amps on each leg of the element, and that works out for my rating of 5600 watts (see, all numbers).
My cooling fan is properly oriented and running at what appears to be full speed, it turns on when the compartment reaches about 120’F. What am I missing? He asks about the time delay and if it is functional, when you turn the oven off it keeps the main fan running for 20 minutes to fully cool everything down. I get off the phone and test the time delay. While I am waiting out that time delay to make sure it runs long enough, I realize how clean everything is in the kitchen. My oven is on a stand with casters and is connected with a cord and plug.
I think you know where I am going with this. One of the closing staff members would shut the oven off, then unplug it and roll it out of the way to fully sweep and mop the floor. Being unplugged meant the cooling fans were off, and the main fan was off, so the heat just built up in the metal and eventually tripped the control box limit. When they plugged it back in, the time delay would run the 20 minutes, but by then, the limit was already open, and when they arrived in the morning to turn it on, nothing happened.
This turned out not to be an issue with the equipment, but with one end-user that was only trying to do the best job they could when cleaning up at night. The only fix here was educating the customer on the cool-down feature and what it was for, and how it worked.
Having all my information in advance before contacting the factory and being able to intelligently relay that information allowed them to narrow down where the issue could be and lead me to a solution immediately. I got my answer, and they got to move on to the next call, win-win.
I’ve found that when training new technicians, if you teach them how, where, and when to take measurements and what the readings mean so they can have a useful conversation with tech support, something great happens. They stop needing to make that call, and tech support becomes just what it was meant to be – support.